Types Of Stone Finishing
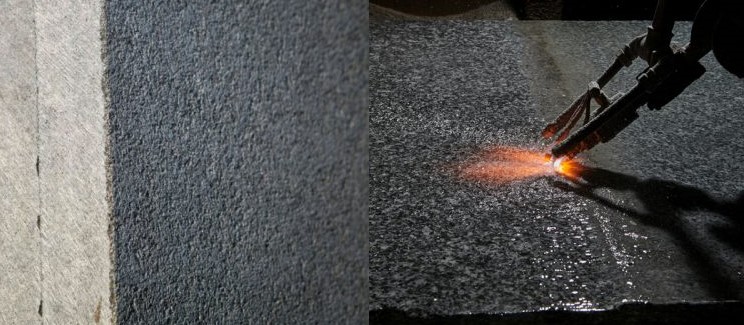
Types Of Stone Finishing
Stone finishing is a crucial phase in stone production and processing. Since various building stones have specific uses in different building parts, stone surfaces must be finished accordingly based on their purpose. For example, some areas require a rough surface to prevent slipping, while others need a glossy surface. For different types of stones, depending on the characteristics of each of them, 24 types of finishing are applicable. This article examines some types of stone surface finishing.
You can learn more about granite finishes in the article below:
- Polished
- Honed
- Flamed
- Leather flamed and flamed brushed
- cut
- Scratched
- Cotton
- Tumbled
- Sawn
- Chiseled
1- Polished
The stone’s most common and most used finish is the polished finish. In this finish, the stone’s surface becomes completely polished and shiny. The most common use of this finish is on stairs, floors (generally interior spaces), and walls of buildings, and it should be avoided for use where it is possible to get wet and slippery.
2- Honed
The stone’s surface is smooth but lacks a shine or light reflection due to its honed finish. This finish is known for appearing more natural and less slippery compared to polished surfaces. Additionally, the stone’s color appears lighter with a honed finish.
3- Flamed
Granite stones with a strong resistance often get this finish. In the flamed finish, the stone’s surface is heated by a torch with a low flame, creating a rough surface that prevents slippage. This finish can be used on the floor of the outside area and surrounding the stairs and pool.
4- Leather Flamed and Flamed Brushed
For a natural and classic look, leather diamond-tipped brushes finish uneven and unpolished stone surfaces. Because of its friction, this type of finish is perfect for flooring, outdoor stairs, swimming pools, sidewalks, bathroom floors, and even kitchen countertops.
By painting the flame-finished stone with special epoxy paint in 3 stages, performing the thermal stabilization process in the oven after each step, and finally removing the stain left on the surface, it is possible to achieve a colored leather-flamed finish.
5- Cut
Producing parallel or diagonal grooves on stone surfaces is called a “cut finish”. The various types of this finish are outlined below:
- Polished Cut
Creating parallel grooves on polished stone is known as a polished cut finish. This finish gives the building’s façade a stunning appearance.
- Irregular Cut
The finish of the stone has an irregular cut with grooves that create an eye-catching effect on the tiles.
- Irregular Sandblast Cut
The irregular sandblast cut involves creating uneven grooves on the stone tiles while adding tiny abrasive particles to smooth out the edges of the grooves and ensure consistent coloring of the tiles.
- Diagonal Cut
Creating diagonal parallel grooves
- Broken Cut
To get a broken-cut finish, make consistent cuts on the stone and break it with a hammer. It’s commonly used on building facades and fountains.
- Sandblast Broken Cut
“Sandblast broken cut” is a stone finish with softer edges and protruding indentations, resulting in a uniform color.
- Hammered Cut
We achieve a rough surface after cutting by using a bush hammer with diamond-tipped brushes. This process creates a visually appealing stone appearance and is often used in the design of fountains and villa facades.
- Flamed Cut
Creating parallel grooves in flamed stone preserves its natural characteristics while providing a high level of friction, making it an excellent option for sloping parking lots.
6- Scratched
A scratched finish on stone is achieved by making small, shallow, parallel grooves, which creates a rough texture.
7- Cotton
The cotton finish stone is achieved by creating horizontally and vertically perpendicular grooves at equal intervals. This results in a surface with high friction and a visually appealing appearance.
8- Tumbled
Using sand, pebbles and water to tumble the surface of the stone in order to create an aged appearance. A finish can be applied to variety of stones to give them the impression that they have been walked on for centuries. This is an aging process similar to the one applied to achieve an antique finish. In this case, natural stone is introduced in a vibrating drum-like machine with smaller, more resistant stones that wear the tile completely.
9- Sawn
This finish is created by “sawing” the stone with diamond disc teeth. It produces a somewhat rough and irregular surface with small furrows and undulations. Sawn finish makes the stone lighter and gives it a matte tone. Sawn finish is available for external paving, steps, pathways, driveways and patios. This surface is a result of sawing, when the granite, marble, sandstone & Travertine block is sawn into slabs by diamond gang saw or by diamond wire saw or by block cutter. The sawn surface is generally smooth but probably some “blade / saw markings” can be seen on the surface of the material.
10- Chiseled
A diamond teeth mill grinder is applied perpendicularly to the surface, to achieve the typical flat profile. The grooves always run parallel, the distance between them remains constant. A chiseled finish is created, as the name implies, by breaking a stone with a hammer and chisel. Depending on the type of chisel used and skill level of the person using it, this can provide a very rough surface or a slightly irregular finish. A chiseled finish can be applied to any stone.
13- Sandblasted
This treatment removes saw marks and achieves a smooth surface with fine, sometimes almost invisible circular marks. The tile looks slightly scratched but feels nice when touched. The colors are a bit dull. This type of finish is usually applied to sandstone and is one of the finishes you can choose for exterior. This finish can also be found under the name grit blasted finish.
14- Bush-Hammered
A highly textured finish best used for external applications such as paving or walkways. A mechanical hammer hits the stone and leaves small indentations on the surface. The result depends on the size of the hammer and the number of points on the hammer. The result leaves the surface of the stone smooth with small indentations.
15- Antiqued
This surface can be achieved by machines that resemble commercial washing machines for smaller items or by first flaming and then using abrasives to brush the surface of larger items. It gives a worn look to the stone and also stimulates its further aging over time.